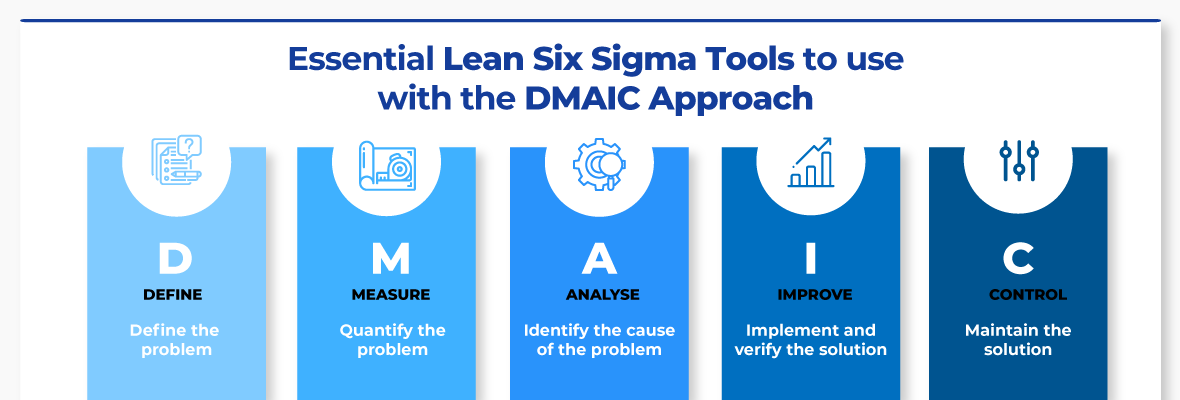
Supply Chain Management Review provides the latest information for business owners interested in improving their supply chain management. This magazine, which is located in the U.S., publishes for almost a year. It discusses issues such the role and changing nature of business models, as well as information technology. The publication is especially useful to large supply chains and companies that are involved in the management of them.
Manufacturing is the last stage of supply chain management
Supply chain management is a complicated process that involves five key elements. They include planning, sourcing raw ingredients, manufacturing, delivery and return, and logistics. For companies to avoid costly bottlenecks, they need to be proficient at all five of these elements. Because perishable goods are fragile, manufacturing is crucial.
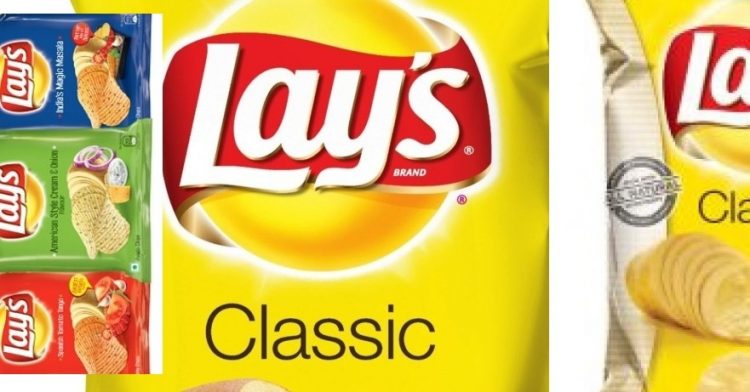
Reverse logistics
The bottom line of any company is dependent on reverse logistics management. This service allows businesses to utilize existing infrastructure to reduce costs, increase efficiency and improve their profitability. The company can benefit from this service by helping them adopt sustainable business models. Reverse logistics comes with its own set of challenges.
Flexible model
Businesses can use a flexible supply network to meet customer demand when there is high and low demand. It is based on part segmentation and accurate stocking algorithms. Flexible planning includes automation on factory floors. Staples is a manufacturer of writing utensils. Because it anticipates an increase in demand during back-to-school, the company stocks up on supplies throughout.
Agile model
A review of the Agile model for supply chain management can be a great way to help organizations make substantial changes and ensure that your supply chain is responsive to new developments. Changes, such as the loss of a significant manufacturing partner or logistical block, can lead to significant delays, but an agile supply chain can overcome these challenges quickly. The model gives stakeholders visibility which allows them to continuously improve their supply chain process. Additionally, organizations can outsource certain segments of their supply chain, which leads to lower costs. It also helps businesses anticipate shortages and reduce overstock inventories.
Model of fast chain
This fast-chain model of supply chain management emphasizes speed, responsiveness, and is best suited for companies that frequently change product lines and compete for the same customers. This model is known for efficient inventory management and maximising the use of production equipment. This model is most suitable for businesses producing trendy products with short life cycles. Businesses that are looking to bring products to market quickly will also benefit from this model.
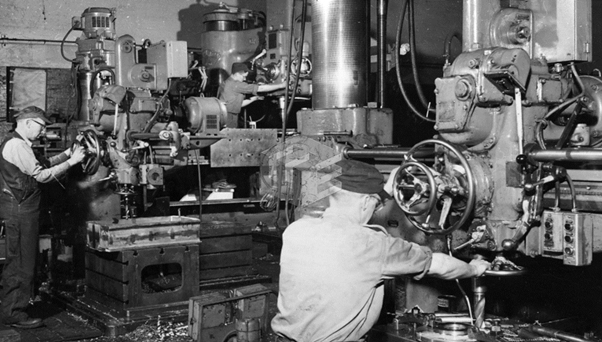
Ethics of supply chain management
Supply chain management ethics has become a key consideration for companies because it can have a major impact on business performance and the bottom line. Supply chain companies face many problems, not just those facing factories and workers. Organizations are taking a variety of steps to ensure ethical supply chains.
FAQ
What does warehouse refer to?
A warehouse or storage facility is where goods are stored before they are sold. It can be either an indoor or outdoor space. Sometimes, it can be both an indoor and outdoor space.
What types of jobs can you find in logistics
There are different kinds of jobs available in logistics. Some of them are:
-
Warehouse workers - They load and unload trucks and pallets.
-
Transportation drivers - They drive trucks and trailers to deliver goods and carry out pick-ups.
-
Freight handlers, - They sort out and pack freight in warehouses.
-
Inventory managers - These are responsible for overseeing the stock of goods in warehouses.
-
Sales representatives - They sell products.
-
Logistics coordinators are responsible for organizing and planning logistics operations.
-
Purchasing agents – They buy goods or services necessary to run a company.
-
Customer service representatives are available to answer customer calls and emails.
-
Shipping clerks – They process shipping orders, and issue bills.
-
Order fillers are people who fill orders based only on what was ordered.
-
Quality control inspectors are responsible for inspecting incoming and outgoing products looking for defects.
-
Others - There are many types of jobs in logistics such as transport supervisors and cargo specialists.
What are the 7 Rs of logistics.
The acronym 7Rs of Logistics refers to the seven core principles of logistics management. It was developed and published by the International Association of Business Logisticians in 2004 as part of the "Seven Principles of Logistics Management".
The following letters make up the acronym:
-
Responsible - ensure that all actions taken are within legal requirements and are not harmful to others.
-
Reliable – have faith in your ability and capability to keep promises.
-
Be responsible - Use resources efficiently and avoid wasting them.
-
Realistic - Consider all aspects of operations, including environmental impact and cost effectiveness.
-
Respectful - Treat people fairly and equitably
-
Reliable - Find ways to save money and increase your productivity.
-
Recognizable is a company that provides customers with value-added solutions.
Statistics
- Job #1 is delivering the ordered product according to specifications: color, size, brand, and quantity. (netsuite.com)
- It's estimated that 10.8% of the U.S. GDP in 2020 was contributed to manufacturing. (investopedia.com)
- In the United States, for example, manufacturing makes up 15% of the economic output. (twi-global.com)
- (2:04) MTO is a production technique wherein products are customized according to customer specifications, and production only starts after an order is received. (oracle.com)
- According to a Statista study, U.S. businesses spent $1.63 trillion on logistics in 2019, moving goods from origin to end user through various supply chain network segments. (netsuite.com)
External Links
How To
How to Use 5S for Increasing Productivity in Manufacturing
5S stands in for "Sort", the "Set In Order", "Standardize", or "Separate". Toyota Motor Corporation was the first to develop the 5S approach in 1954. It improves the work environment and helps companies to achieve greater efficiency.
The basic idea behind this method is to standardize production processes, so they become repeatable, measurable, and predictable. This means that every day tasks such cleaning, sorting/storing, packing, and labeling can be performed. This knowledge allows workers to be more efficient in their work because they are aware of what to expect.
There are five steps to implementing 5S, including Sort, Set In Order, Standardize, Separate and Store. Each step requires a different action to increase efficiency. For example, when you sort things, you make them easy to find later. When you set items in an order, you put items together. Then, after you separate your inventory into groups, you store those groups in containers that are easy to access. You can also label your containers to ensure everything is properly labeled.
This requires employees to critically evaluate how they work. Employees need to understand the reasons they do certain jobs and determine if there is a better way. In order to use the 5S system effectively, they must be able to learn new skills.
The 5S Method not only improves efficiency, but it also helps employees to be more productive and happier. As they begin to see improvements, they feel motivated to continue working towards the goal of achieving higher levels of efficiency.