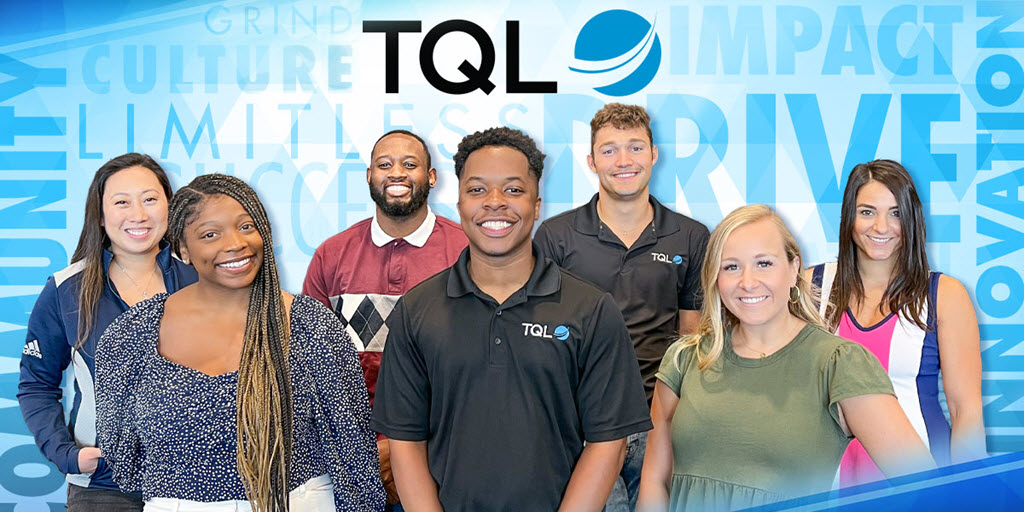
Durable goods have items that don't wear out quickly and can provide utility for a prolonged period. They are not like nondurable products, which can be used only once. They will provide greater or equal utility over time. For example, a durable car will continue to serve you for years.
Nondurable goods may be consumed immediately
Nondurable goods, unlike durable goods, have a short lifespan and are usually consumed quickly. In recessions, consumers are more likely to continue purchasing nondurable goods than to spend on durable goods. These items have lower prices and can be paid with cash. Examples of nondurable items include meat, fruits, vegetable, dairy products and bakery products. Others include dish soap, detergent, and cosmetics.
In general, nondurable goods are the least expensive types of goods, lasting less than three years. They are also purchased relatively often, allowing consumers to buy them frequently without concern for their future value. Most nondurable goods are also disposable and can be bought only one time, such as packaged food and laundry detergent. However, service goods are intangible and are created in response to customer needs. The perception of a product by consumers is what drives their purchase decisions. This perception can change depending on the product's price.
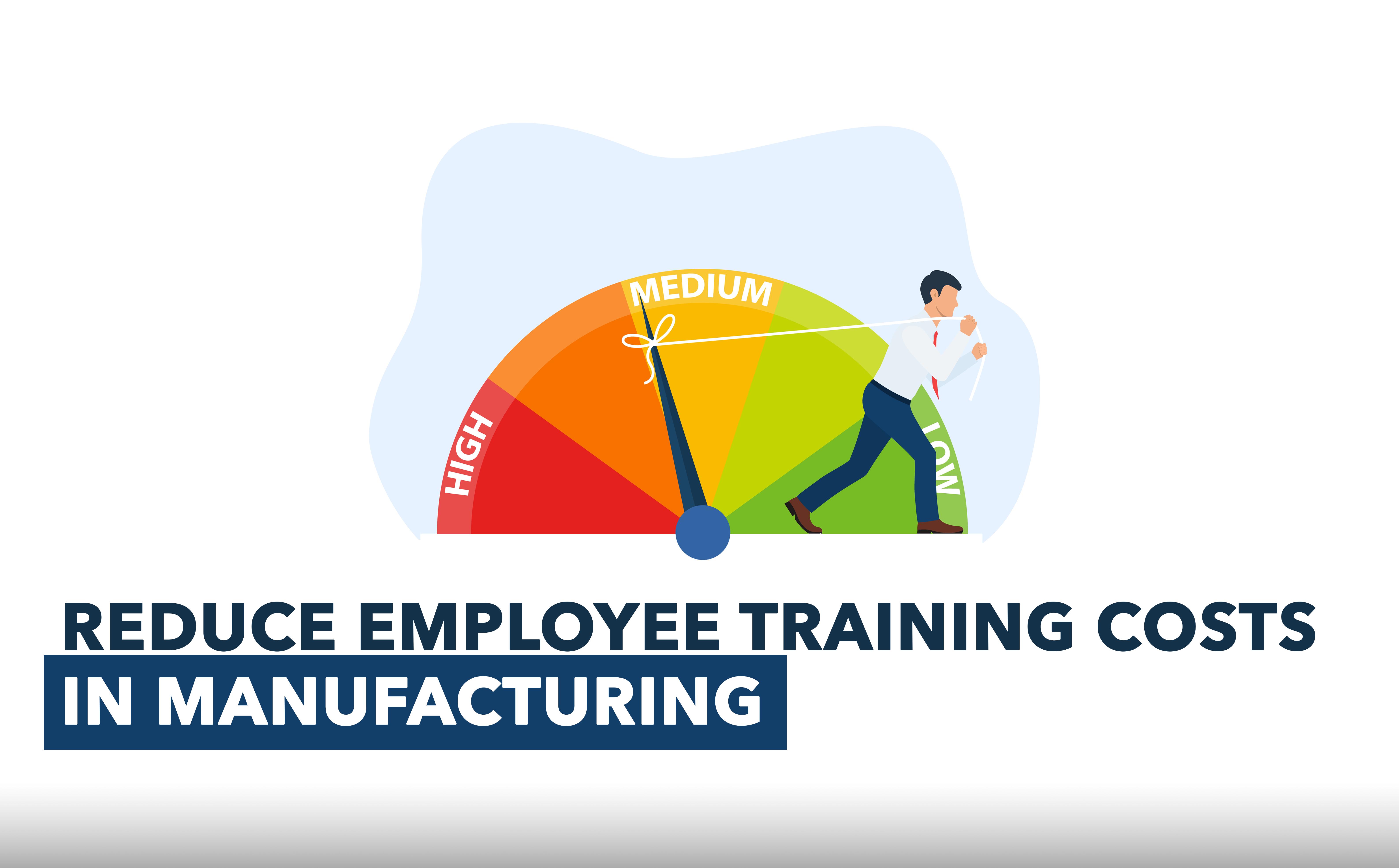
Durable goods on the other side are those products that will provide a continuous stream of utility over time. These products are often called consumer durables. They include automobiles, household furniture, sporting items, and jewelry. Durables are usually purchased during economic growth. Nondurables, however, can be purchased when the economy is in recession.
Durable goods last more than a year
Durable goods refer to tangible commodities that can last for at most one year when used as intended. They can be divided into two categories: consumer durables and producer durables. Consumer durables consist of household goods, such as cars, boats and furniture. Producer durability includes machinery, appliances, and fine jewellery.
Durable goods are expected last for at least 3 years but may require repair or servicing. Durable goods are designed to be durable and last for many years. With proper care and maintenance, durable goods can last up to 20 years.
Durable goods are often an indicator of economic growth. An increase in durable goods sales can result in higher employment and better returns on investment. Conversely, declining sales of durable goods may signal a decline in economic activity. This could indicate that consumers are spending less money on new goods and more on repairs or servicing their existing products. This could result in a decline in durable goods, which may cause a recession.
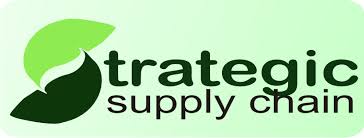
Impact of COVID-19 pandemic on durable goods
COVID-19, which was a pandemic that brought about widespread illness, has had a significant impact on consumer spending. People became more cautious about going to the gym and avoiding social gatherings as a result. Also, they stopped hailing cabs which resulted to decreased consumer spending. Instead, people spent more time at their homes doing home production and leisure activities. This in turn reduced consumer spending on restaurants and other services.
The US economy was impacted by the COVID-19 Pandemic in a significant way. The disease not only increased the demand for durable goods but also prompted strong fiscal policies to increase household disposable income. This effect may have been responsible for half of 2020's rise in durable goods consumption.
The COVID-19 Pandemic has impacted individuals, communities, as well as businesses. While the impact on fast-moving goods has received much attention, less coverage has focused on the impact of the disease on durable goods. NielsenIQ BASES recently conducted a survey that revealed that nearly a third of respondents have made durables purchases in response. The disease is also affecting many consumers' buying habits, as they spend more time at their homes with their children.
FAQ
How can we reduce manufacturing overproduction?
In order to reduce excess production, you need to develop better inventory management methods. This would decrease the time that is spent on inefficient activities like purchasing, storing, or maintaining excess stock. This would allow us to use our resources for more productive tasks.
One way to do this is to adopt a Kanban system. A Kanban board is a visual display used to track work in progress. In a Kanban system, work items move through a sequence of states until they reach their final destination. Each state is assigned a different priority.
When work is completed, it can be transferred to the next stage. It is possible to keep a task in the beginning stages until it gets to the end.
This helps to keep work moving forward while ensuring that no work is left behind. Managers can monitor the work being done by Kanban boards to see what is happening at any given time. This data allows them adjust their workflow based upon real-time data.
Lean manufacturing, another method to control inventory levels, is also an option. Lean manufacturing emphasizes eliminating waste in all phases of production. Waste includes anything that does not add value to the product. The following are examples of common waste types:
-
Overproduction
-
Inventory
-
Packaging that is not necessary
-
Overstock materials
Manufacturers can reduce their costs and improve their efficiency by using these ideas.
How can manufacturing avoid production bottlenecks
Avoiding production bottlenecks is as simple as keeping all processes running smoothly, from the time an order is received until the product ships.
This includes planning for capacity requirements as well as quality control measures.
Continuous improvement techniques like Six Sigma are the best way to achieve this.
Six Sigma is a management system used to improve quality and reduce waste in every aspect of your organization.
It's all about eliminating variation and creating consistency in work.
What is manufacturing and logistics?
Manufacturing refers to the process of making goods using raw materials and machines. Logistics covers all aspects involved in managing supply chains, including procurement and production planning. Manufacturing and logistics can often be grouped together to describe a larger term that covers both the creation of products, and the delivery of them to customers.
What is the importance of automation in manufacturing?
Automating is not just important for manufacturers, but also for service providers. They can provide services more quickly and efficiently thanks to automation. It reduces human errors and improves productivity, which in turn helps them lower their costs.
What skills should a production planner have?
A production planner must be organized, flexible, and able multitask to succeed. You must also be able to communicate effectively with clients and colleagues.
What is production planning?
Production Planning is the creation of a plan to cover all aspects, such as scheduling, budgeting. Location, crew, equipment, props and other details. This document aims to ensure that everything is planned and ready when you are ready to shoot. This document should include information about how to achieve the best results on-set. This includes location information, crew details, equipment specifications, and casting lists.
The first step in filming is to define what you want. You may have decided where to shoot or even specific locations you want to use. Once you've identified the locations and scenes you want to use, you can begin to plan what elements you need for each scene. You might decide you need a car, but not sure what make or model. In this case, you could start looking up cars online to find out what models are available and then narrow your choices by choosing between different makes and models.
Once you have found the right car, you can start thinking about extras. What about additional seating? Or maybe you just need someone to push the car around. You may want to change the interior's color from black or white. These questions can help you decide the right look for your car. It is also worth considering the types of shots that you wish to take. Will you be filming close-ups or wide angles? Maybe the engine or steering wheel is what you are looking to film. These things will help you to identify the car that you are looking for.
Once you have determined all of the above, you can move on to creating a schedule. You will know when you should start and when you should finish shooting. A schedule for each day will detail when you should arrive at the location and when you need leave. This way, everyone knows what they need to do and when. Book extra staff ahead of time if you need them. It is not worth hiring someone who won’t show up because you didn’t tell him.
It is important to calculate the amount of filming days when you are creating your schedule. Some projects may only take a couple of days, while others could last for weeks. When creating your schedule, be aware of whether you need more shots per day. Multiple shots at the same location can increase costs and make it more difficult to complete. It is better to be cautious and take fewer shots than you risk losing money if you are not sure if multiple takes are necessary.
Budgeting is another crucial aspect of production plan. A realistic budget will help you work within your means. Keep in mind that you can always reduce your budget if you face unexpected difficulties. But, don't underestimate how much money you'll spend. If you underestimate how much something costs, you'll have less money to pay for other items.
Planning production is a tedious process. Once you have a good understanding of how everything works together, planning future projects becomes easy.
What are the four types in manufacturing?
Manufacturing refers the process of turning raw materials into useful products with machines and processes. It can involve many activities like designing, manufacturing, testing packaging, shipping, selling and servicing.
Statistics
- Job #1 is delivering the ordered product according to specifications: color, size, brand, and quantity. (netsuite.com)
- In the United States, for example, manufacturing makes up 15% of the economic output. (twi-global.com)
- In 2021, an estimated 12.1 million Americans work in the manufacturing sector.6 (investopedia.com)
- According to the United Nations Industrial Development Organization (UNIDO), China is the top manufacturer worldwide by 2019 output, producing 28.7% of the total global manufacturing output, followed by the United States, Japan, Germany, and India.[52][53] (en.wikipedia.org)
- Many factories witnessed a 30% increase in output due to the shift to electric motors. (en.wikipedia.org)
External Links
How To
Six Sigma in Manufacturing
Six Sigma can be described as "the use of statistical process control (SPC), techniques to achieve continuous improvement." Motorola's Quality Improvement Department developed it at their Tokyo plant in Japan in 1986. The basic idea behind Six Sigma is to improve quality by improving processes through standardization and eliminating defects. In recent years, many companies have adopted this method because they believe there is no such thing as perfect products or services. Six Sigma aims to reduce variation in the production's mean value. This means that if you take a sample of your product, then measure its performance against the average, you can find out what percentage of the time the process deviates from the norm. If this deviation is too big, you know something needs fixing.
Understanding how your business' variability is a key step towards Six Sigma implementation is the first. Once you understand that, it is time to identify the sources of variation. These variations can also be classified as random or systematic. Random variations happen when people make errors; systematic variations are caused externally. If you make widgets and some of them end up on the assembly line, then those are considered random variations. But if you notice that every widget you make falls apart at the exact same place each time, this would indicate that there is a problem.
Once you have identified the problem, you can design solutions. That solution might involve changing the way you do things or redesigning the process altogether. Once you have implemented the changes, it is important to test them again to ensure they work. If they didn't work, then you'll need to go back to the drawing board and come up with another plan.