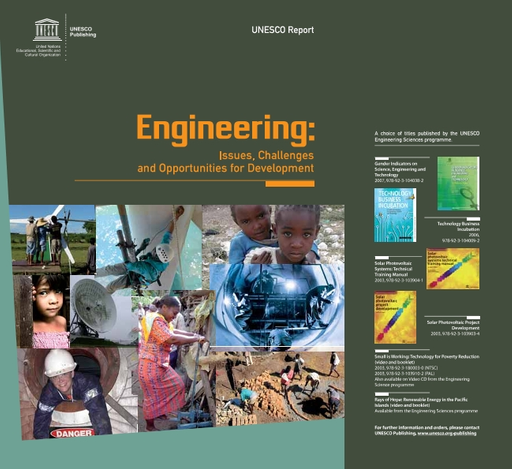
Chemical manufacturing is a major US industry. It transforms organic or inorganic materials into useful products. It supplies products and materials for industries, ranging from plastics through explosives. Chemical industry also faces many problems. Numerous workers are at high risk for health and safety.
Chemical manufacturing is organized into two main segments: commodity chemicals and specialty chemicals. These two segments share the same infrastructure and processes. The types of products they produce are however different. Specialty chemical are often designed to be used by customers. Specialty producers produce some of most expensive chemicals. Many of these chemicals are protected by patents.
Some chemicals can be produced in one location, but most petrochemicals as well as commodity chemicals are made in large-scale facilities. Rotterdam in The Netherlands and Texas are three examples of large-scale chemical facilities. Large-scale chemical plants often share utilities and other infrastructures which creates economies of scale.
The United States is the second-largest chemical manufacturer in the world behind China. Statista estimates that the annual value of the chemical industry exceeds $4 trillion. The top 50 US companies account for roughly half of the revenue in the industry.
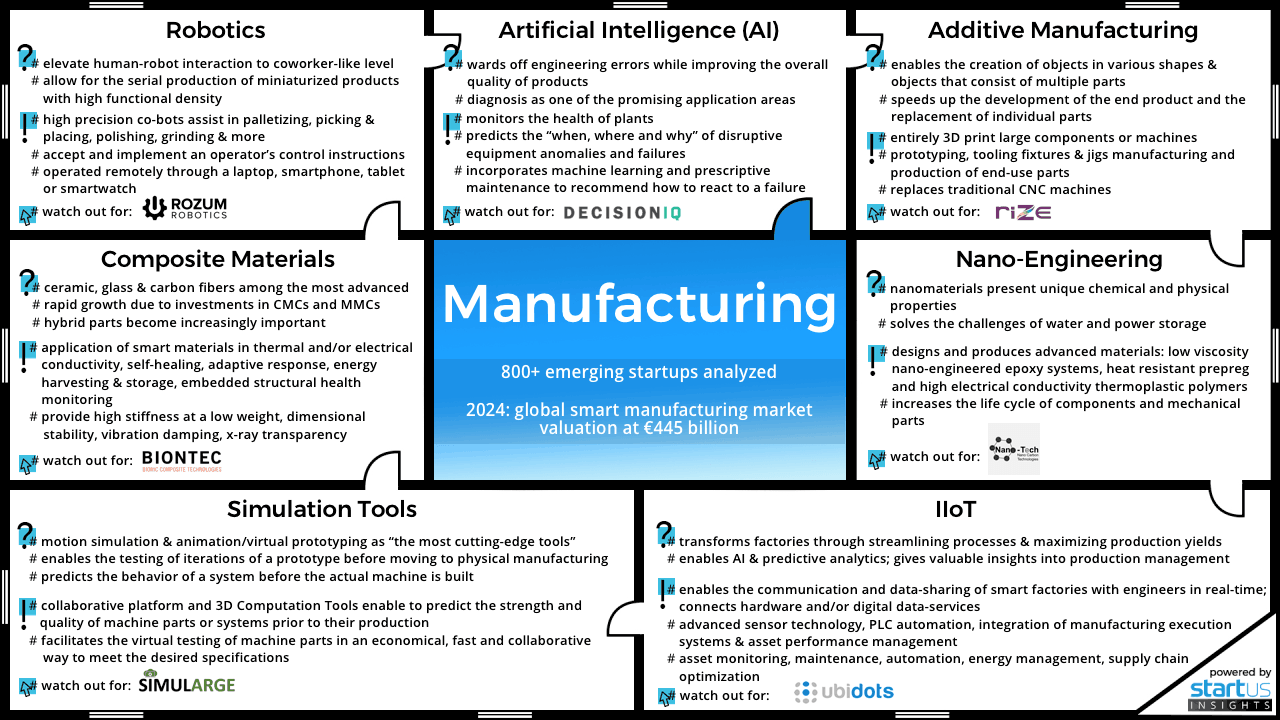
The chemical manufacturing industry employs approximately 20 million people worldwide. Many of these workers work in large-scale plants, but a few are contract or part-time employees. Increasing competition and technological advances have had a negative impact on the industry's employment.
The demand for chemicals is driven by the overall U.S. economy. The chemical sector is highly regulated. Governing bodies set regulations and standards for the manufacturing process. Companies need to implement sustainable manufacturing practices. Additionally, some chemical manufacturing raw materials are dangerous to extract.
The industry faces difficult procurement challenges. A high cost of raw material acquisition is another problem. Some companies move their operations to lower-cost locations in order to keep costs down. A few companies have also begun to merge with other companies or moved their production activities into developing countries. This will lead to the loss of jobs.
In 2008, basic chemical manufacturing accounted for 80 percent. This group is composed of manufacturers of pesticides, dyes, and other materials. Pfizer, Dow, and BASF are the most prominent manufacturers in this segment. DuPont is also a major player, as well as Formosa Plastics & Sinopec Group.
Large-scale production facilities can usually be kept clean. Workers are required to wear safety goggles and work in a temperature-controlled environment. However, some workers can be replaced with sophisticated machines controlled by computers. Many of these workers work nights.
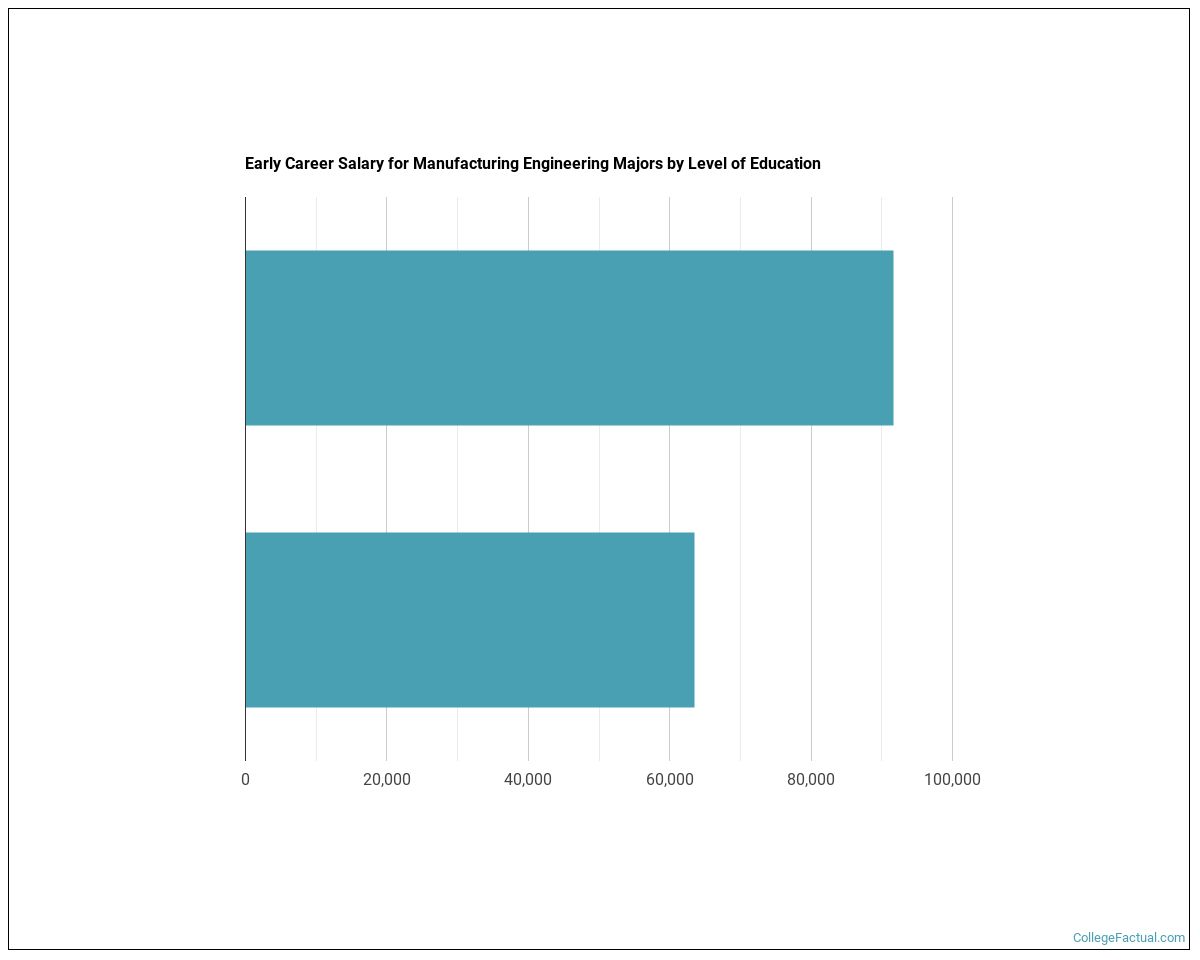
It is possible that chemical manufacturing plants will need to adapt to new production methods. New processes can improve accuracy and reduce labor costs. Nanotechnology will also make chemical manufacturing more efficient. Nanotechnology can also be used to reduce waste and energy consumption.
The employment prospects for the chemical manufacturing industry will be affected by increased foreign competition, technological developments, as well as safety and environmental concerns. Generally, the industry's employment is projected to decrease 13 percent over the next four years.
FAQ
What are the four types in manufacturing?
Manufacturing is the process of transforming raw materials into useful products using machines and processes. It involves many different activities such as designing, building, testing, packaging, shipping, selling, servicing, etc.
Why is logistics important in manufacturing
Logistics are essential to any business. They can help you achieve great success by helping you manage product flow from raw material to finished goods.
Logistics play an important role in reducing costs as well as increasing efficiency.
What can I do to learn more about manufacturing?
Practical experience is the best way of learning about manufacturing. If that is not possible, you could always read books or view educational videos.
What are the responsibilities of a production planner
A production planner ensures all aspects of the project are delivered on time, within budget, and within scope. They ensure that the product or service is of high quality and meets client requirements.
Are there ways to automate parts of manufacturing?
Yes! Yes. Automation has been around since ancient time. The Egyptians invented the wheel thousands of years ago. Robots are now used to assist us in assembly lines.
Actually, robotics can be used in manufacturing for many purposes. These include:
-
Line robots
-
Robot welding
-
Robot painting
-
Robotics inspection
-
Robots that make products
Automation could also be used to improve manufacturing. For example, 3D printing allows us to make custom products without having to wait for weeks or months to get them manufactured.
Statistics
- Many factories witnessed a 30% increase in output due to the shift to electric motors. (en.wikipedia.org)
- In 2021, an estimated 12.1 million Americans work in the manufacturing sector.6 (investopedia.com)
- (2:04) MTO is a production technique wherein products are customized according to customer specifications, and production only starts after an order is received. (oracle.com)
- It's estimated that 10.8% of the U.S. GDP in 2020 was contributed to manufacturing. (investopedia.com)
- According to the United Nations Industrial Development Organization (UNIDO), China is the top manufacturer worldwide by 2019 output, producing 28.7% of the total global manufacturing output, followed by the United States, Japan, Germany, and India.[52][53] (en.wikipedia.org)
External Links
How To
How to use the Just In-Time Production Method
Just-in-time (JIT) is a method that is used to reduce costs and maximize efficiency in business processes. It is a process where you get the right amount of resources at the right moment when they are needed. This means that you only pay the amount you actually use. Frederick Taylor developed the concept while working as foreman in early 1900s. Taylor observed that overtime was paid to workers if they were late in working. He realized that workers should have enough time to complete their jobs before they begin work. This would help increase productivity.
JIT is about planning ahead. You should have all the necessary resources ready to go so that you don’t waste money. It is important to look at your entire project from beginning to end and ensure that you have enough resources to handle any issues that may arise. If you expect problems to arise, you will be able to provide the necessary equipment and personnel to address them. This way, you won't end up paying extra money for things that weren't really necessary.
There are many JIT methods.
-
Demand-driven: This type of JIT allows you to order the parts/materials required for your project on a regular basis. This will enable you to keep track of how much material is left after you use it. It will also allow you to predict how long it takes to produce more.
-
Inventory-based: This is a type where you stock the materials required for your projects in advance. This allows you to predict how much you can expect to sell.
-
Project-driven: This means that you have enough money to pay for your project. When you know how much you need, you'll purchase the appropriate amount of materials.
-
Resource-based JIT: This type of JIT is most commonly used. Here you can allocate certain resources based purely on demand. For instance, if you have a lot of orders coming in, you'll assign more people to handle them. You'll have fewer orders if you have fewer.
-
Cost-based: This approach is very similar to resource-based. However, you don't just care about the number of people you have; you also need to consider how much each person will cost.
-
Price-based: This is very similar to cost-based, except that instead of looking at how much each individual worker costs, you look at the overall price of the company.
-
Material-based is an alternative to cost-based. Instead of looking at the total cost in the company, this method focuses on the average amount of raw materials that you consume.
-
Time-based: Another variation of resource-based JIT. Instead of focusing solely on the amount each employee costs, focus on how long it takes for the project to be completed.
-
Quality-based JIT: This is another variation of resource based JIT. Instead of looking at the labor costs and time it takes to make a product, think about its quality.
-
Value-based JIT: One of the most recent forms of JIT. This is where you don't care about how the products perform or whether they meet customers' expectations. Instead, you're focused on how much value you add to the market.
-
Stock-based: This inventory-based approach focuses on how many items are being produced at any one time. This method is useful when you want to increase production while decreasing inventory.
-
Just-intime planning (JIT), is a combination JIT/sales chain management. This refers to the scheduling of the delivery of components as soon after they are ordered. It reduces lead times and improves throughput.