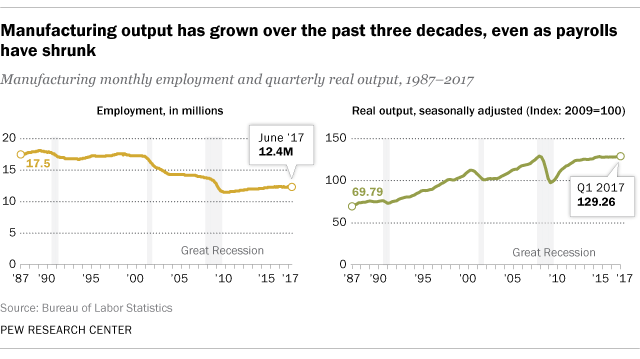
General managers have the responsibility of developing strategy, identifying and hiring functional leaders, as well as communicating with company stakeholders. This article will provide an overview of the various responsibilities and skills needed to excel in this job. Read on to see a complete description of the duties of a general manger. Strong communication and presentation skills are essential for a successful general management role. Financial management skills are also essential. Ultimately, your success depends on your persistence and ability to manage your company's performance and processes within a budget. You must be a great leader and build trust with customers.
Strategy formulation falls under the control of the GMs
Although it is true that GMs are responsible for strategy formulation, the process can be subject to certain risks. One example is a GM that is motivated by self or a member of a team, and may overplay their part in strategy formulation. Managers are subjected primarily to their own motivations.
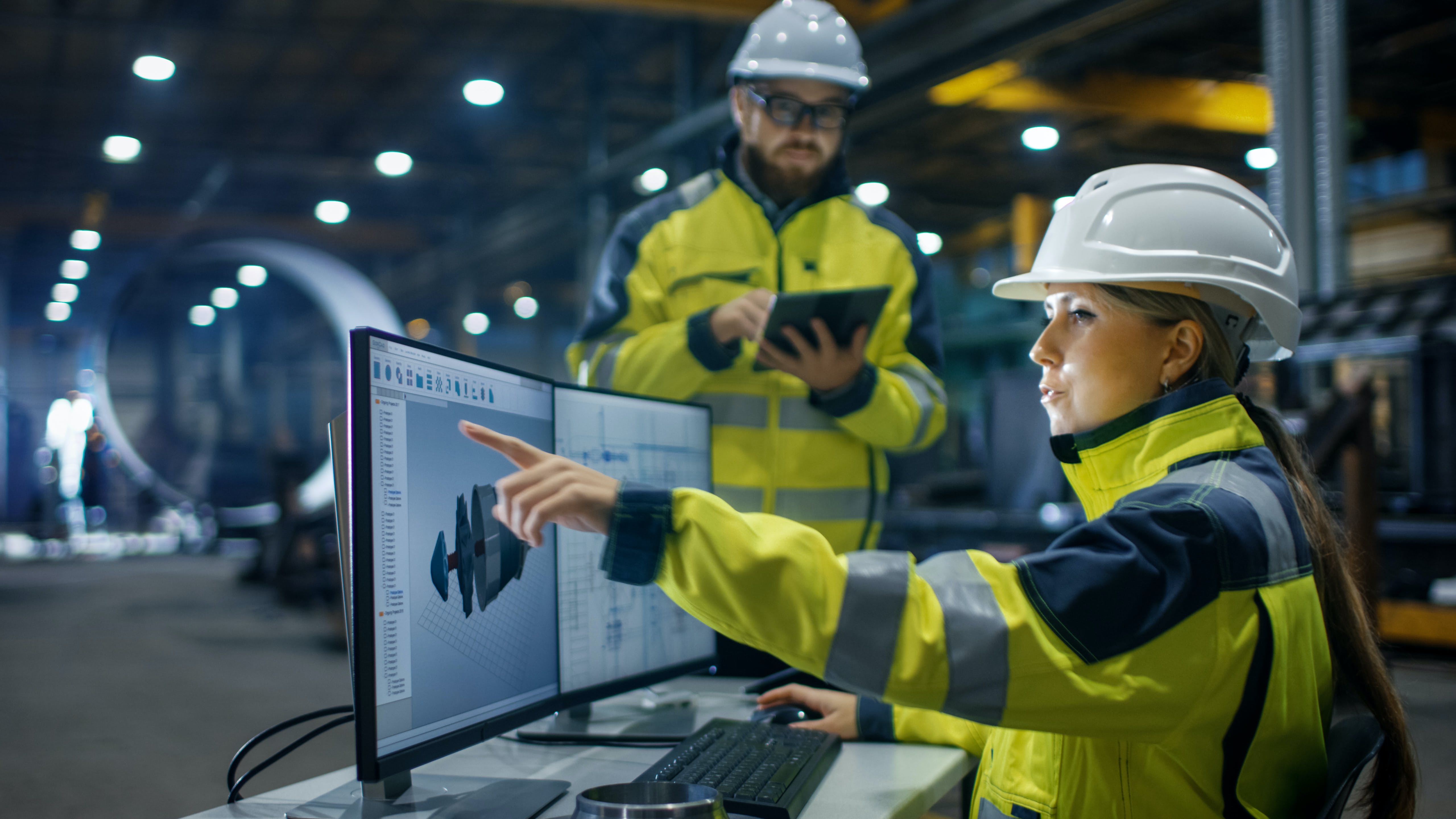
They recruit functional leaders
General managers are responsible for all aspects of the organization and its business units. They oversee the management of all aspects within the business, from structure and budgets to people. They are responsible for managing the daily operations of each business unit, as well as coordinating key performance goals across all departments. This position requires them to speak the language of finance, human resources, and sales to successfully execute the strategy. The role of general manager is complex and essential for the overall success of an organisation.
They work closely together with their subordinates
A general manager's job requires them to understand the internal workings of the organization and communicate with all the departments. They need to be analytically able to spot problems and provide solutions. The role of the general manager is to manage tasks and ensure employees do their best. It is also important for general managers to communicate clearly with subordinates and work in close collaboration with other departments.
They communicate with each other
Communication skills play a significant role in many general manager duties. General managers can practice listening to employees' concerns and needs by hosting training sessions or coaching employees in effective communication techniques. They can also host more team meetings and social events to foster greater communication. These tips will help you improve your communication skills as a manager. Every manager should be available to their employees in order to make them successful. This is a key part of their job description. They should also be available to answer queries and offer guidance when required.
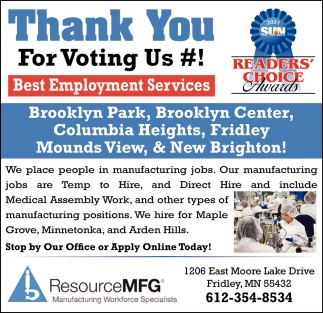
They are motivating
The top GMs are able and willing to motivate staff. They are willing and able to work overtime, demonstrate dedication to the company, and set an example for others. They also encourage their staff to live up to their high standards. Here are some ways that top managers motivate their staff.
FAQ
What is meant by manufacturing industries?
Manufacturing Industries are those businesses that make products for sale. The people who buy these products are called consumers. These companies use a variety processes such as distribution, retailing and management to accomplish their purpose. They make goods from raw materials with machines and other equipment. This includes all types of manufactured goods, including food items, clothing, building supplies, furniture, toys, electronics, tools, machinery, vehicles, pharmaceuticals, medical devices, chemicals, and many others.
What are the products and services of logistics?
Logistics is the process of moving goods from one point to another.
They include all aspects of transport, including packaging, loading, transporting, unloading, storing, warehousing, inventory management, customer service, distribution, returns, and recycling.
Logisticians ensure that the product is delivered to the correct place, at the right time, and under safe conditions. They help companies manage their supply chain efficiency by providing information on demand forecasts, stock levels, production schedules, and availability of raw materials.
They keep track and monitor the transit of shipments, maintain quality standards, order replenishment and inventories, coordinate with suppliers, vendors, and provide support for sales and marketing.
How can manufacturing avoid production bottlenecks
To avoid production bottlenecks, ensure that all processes run smoothly from the moment you receive your order to the time the product ships.
This includes planning to meet capacity requirements and quality control.
Continuous improvement techniques such Six Sigma can help you achieve this.
Six Sigma management is a system that improves quality and reduces waste within your organization.
It emphasizes consistency and eliminating variance in your work.
How important is automation in manufacturing?
Automation is essential for both manufacturers and service providers. They can provide services more quickly and efficiently thanks to automation. They can also reduce their costs by reducing human error and improving productivity.
What is production planning?
Production Planning is the creation of a plan to cover all aspects, such as scheduling, budgeting. Location, crew, equipment, props and other details. This document will ensure everything is in order and ready to go when you need it. This document should include information about how to achieve the best results on-set. This includes information on shooting times, locations, cast lists and crew details.
The first step is to outline what you want to film. You might have an idea of where you want to film, or you may have specific locations or sets in mind. Once you have identified your locations and scenes it's time to begin figuring out what elements you will need for each one. If you decide you need a car and don't know what model to choose, this could be an example. To narrow your options, you can search online for available models.
After you have chosen the right car, you will be able to begin thinking about accessories. What about additional seating? Or maybe you just need someone to push the car around. Maybe you want to change the interior color from black to white? These questions will help you determine the exact look and feel of your car. It is also worth considering the types of shots that you wish to take. Do you want to film close-ups, or wider angles? Maybe you want to show your engine or the steering wheel. This will allow you to determine the type of car you want.
Once you have made all the necessary decisions, you can start to create a schedule. You can use a schedule to determine when and where you need it to be shot. You will need to know when you have to be there, what time you have to leave and when your return home. This way, everyone knows what they need to do and when. If you need to hire extra staff, you can make sure you book them in advance. It's not worth paying someone to show up if you haven't told him.
You will need to factor in the days that you have to film when creating your schedule. Some projects may only take a couple of days, while others could last for weeks. When creating your schedule, be aware of whether you need more shots per day. Multiplying takes in the same area will result both in increased costs and a longer time. If you aren't sure whether you need multiple shots, it is best to take fewer photos than you would like.
Budget setting is an important part of production planning. A realistic budget will help you work within your means. Remember that you can always reduce the budget later on if you run into unforeseen problems. It is important to not overestimate how much you will spend. If you underestimate the cost of something, you will have less money left after paying for other items.
Production planning is a complicated process. But once you understand how everything works together, it becomes much easier to plan future project.
Statistics
- Many factories witnessed a 30% increase in output due to the shift to electric motors. (en.wikipedia.org)
- (2:04) MTO is a production technique wherein products are customized according to customer specifications, and production only starts after an order is received. (oracle.com)
- Job #1 is delivering the ordered product according to specifications: color, size, brand, and quantity. (netsuite.com)
- In the United States, for example, manufacturing makes up 15% of the economic output. (twi-global.com)
- According to the United Nations Industrial Development Organization (UNIDO), China is the top manufacturer worldwide by 2019 output, producing 28.7% of the total global manufacturing output, followed by the United States, Japan, Germany, and India.[52][53] (en.wikipedia.org)
External Links
How To
How to use Lean Manufacturing in the production of goods
Lean manufacturing refers to a method of managing that seeks to improve efficiency and decrease waste. It was developed in Japan during the 1970s and 1980s by Taiichi Ohno, who received the Toyota Production System (TPS) award from TPS founder Kanji Toyoda. Michael L. Watkins published the first book on lean manufacturing in 1990.
Lean manufacturing is often defined as a set of principles used to improve the quality, speed, and cost of products and services. It emphasizes the elimination of defects and waste throughout the value stream. Lean manufacturing is called just-in-time (JIT), zero defect, total productive maintenance (TPM), or 5S. Lean manufacturing eliminates non-value-added tasks like inspection, rework, waiting.
Lean manufacturing improves product quality and costs. It also helps companies reach their goals quicker and decreases employee turnover. Lean Manufacturing is one of the most efficient ways to manage the entire value chains, including suppliers and customers as well distributors and retailers. Lean manufacturing practices are widespread in many industries. Toyota's philosophy is a great example of this. It has helped to create success in automobiles as well electronics, appliances and healthcare.
Five basic principles of Lean Manufacturing are included in lean manufacturing
-
Define value - Find out what your business contributes to society, and what makes it different from other competitors.
-
Reduce waste - Get rid of any activity that does not add value to the supply chain.
-
Create Flow. Ensure that your work is uninterrupted and flows seamlessly.
-
Standardize and Simplify – Make processes as consistent, repeatable, and as simple as possible.
-
Develop Relationships: Establish personal relationships both with internal and external stakeholders.
Although lean manufacturing isn't a new concept in business, it has gained popularity due to renewed interest in the economy after the 2008 global financial crisis. Many companies have adopted lean manufacturing methods to increase their marketability. According to some economists, lean manufacturing could be a significant factor in the economic recovery.
With many benefits, lean manufacturing is becoming more common in the automotive industry. These benefits include increased customer satisfaction, reduced inventory levels and lower operating costs.
The principles of lean manufacturing can be applied in almost any area of an organization. It is especially useful for the production aspect of an organization, as it ensures that every step in the value chain is efficient and effective.
There are three types principally of lean manufacturing:
-
Just-in Time Manufacturing (JIT), also known as "pull system": This form of lean manufacturing is often referred to simply as "pull". JIT is a method in which components are assembled right at the moment of use, rather than being manufactured ahead of time. This approach reduces lead time, increases availability and reduces inventory.
-
Zero Defects Manufacturing (ZDM),: ZDM is a system that ensures no defective units are left the manufacturing facility. If a part needs to be fixed during the assembly line, it should be repaired rather than scrapped. This is also true for finished products that require minor repairs before shipping.
-
Continuous Improvement (CI): CI aims to improve the efficiency of operations by continuously identifying problems and making changes in order to eliminate or minimize waste. It involves continuous improvement of processes, people, and tools.