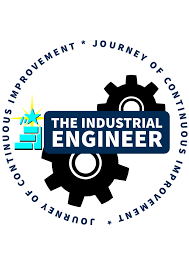
A job director is responsible for job manufacturing. The responsibilities and duties of a job manager are the same as those of a manufacturing associate. This article will cover the requirements for a job manager in manufacturing. To be able to perform various operations, this position requires a skilled workforce. It is important to have an irregular workflow. This will make it easier to manage projects, track development, and help with project management. This production line requires a highly skilled workforce. Employees must be able maintain pace and deliver quality products at the right time.
Job director for manufacturing
Job directors of manufacturing are responsible for overseeing the daily operations of a unit of manufacturing. They are responsible for ensuring products are produced on time and to a high level of quality. In order to develop a new product, the director of manufacturing should work closely with engineers. Before a product goes into large-scale production, they have to assess its feasibility, market fit and impact on processes as well as quality. Also, a director in manufacturing must be able to demonstrate leadership skills. They should have the ability to supervise employees and make improvements to processes and equipment.
Typically, directors of manufacturing hold a bachelor's degree or higher. However, many employers prefer to hire candidates with advanced degrees. Directors of manufacturing should also have at least five year experience in management. Candidates should be able and willing to learn quickly.
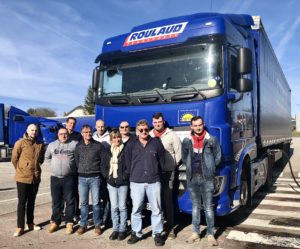
A manufacturing associate's duties
Although the duties of a manufacturing associate are varied, they often involve repetitive motions and assembly line work. Associate must be able to use proper body mechanics and keep in good physical shape to avoid injury. They may have to lift heavy items or stand for long periods.
Duties of a manufacturing associate can range from inspecting parts to reading engineering drawings and executing manufacturing documents. They are expected to work with other members of a team and produce reports. They need to be organised, detail-oriented, efficient communicators, and have prior experience in manufacturing.
A major responsibility is also to ensure quality control for manufactured items. They need to have an understanding of manufacturing processes and the ability to assess whether products meet company standards. They will also need to observe the final products and detect any quality issues.
Qualifications required to become a job-director in manufacturing
A job as a director of manufacturing requires you to be in charge of all the operations in a manufacturing unit, from creating schedules to overseeing the production of products. This role requires you to maintain high quality standards, implement and evaluate new methods to reduce costs, and also to keep them in line with established industry norms. As a director of manufacturing, you will also be responsible to evaluate all staff members. For a job as a director in manufacturing, you will need to demonstrate leadership, organizational skills and problem solving.
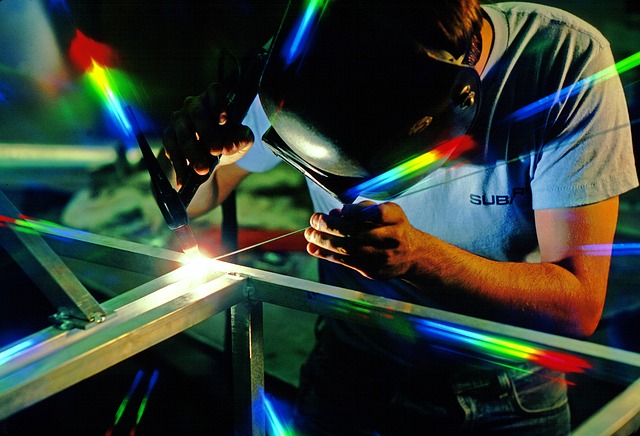
As a manufacturing manager, you will collaborate with engineers and other designers to develop products or services for the company. Excellent communication skills are essential to ensure that everyone in the company is on the right page and understands their respective roles. The ability to communicate effectively will allow you to manage the entire company. As a director for manufacturing, you will need to mentor and coach employees. Training employees on safety protocols and risk mitigation will be a requirement.
FAQ
What are the 4 types manufacturing?
Manufacturing refers to the transformation of raw materials into useful products by using machines and processes. It includes many different activities like designing, building and testing, packaging, shipping and selling, as well as servicing.
What are the 7 Rs of logistics.
The acronym "7R's" of Logistics stands for seven principles that underpin logistics management. It was developed by International Association of Business Logisticians (IABL), and published as part of their "Seven Principles of Logistics Management Series" in 2004.
The following letters make up the acronym:
-
Responsible – ensure that all actions are legal and don't cause harm to anyone else.
-
Reliable - You can have confidence that you will fulfill your promises.
-
Use resources effectively and sparingly.
-
Realistic - Take into consideration all aspects of operations including cost-effectiveness, environmental impact, and other factors.
-
Respectful - Treat people fairly and equitably
-
Responsive - Look for ways to save time and increase productivity.
-
Recognizable: Provide customers with value-added service
Why automate your warehouse
Modern warehousing is becoming more automated. E-commerce has increased the demand for quicker delivery times and more efficient processes.
Warehouses must be able to quickly adapt to changing demands. In order to do this, they need to invest in technology. Automation warehouses can bring many benefits. Here are some benefits of investing in automation
-
Increases throughput/productivity
-
Reduces errors
-
Accuracy is improved
-
Safety Boosts
-
Eliminates bottlenecks
-
Allows companies to scale more easily
-
Makes workers more efficient
-
This gives you visibility into what happens in the warehouse
-
Enhances customer experience
-
Improves employee satisfaction
-
Reduces downtime and improves uptime
-
This ensures that quality products are delivered promptly
-
Removes human error
-
This helps to ensure compliance with regulations
How can I find out more about manufacturing?
Hands-on experience is the best way to learn more about manufacturing. If that is not possible, you could always read books or view educational videos.
What does warehouse mean?
A warehouse, or storage facility, is where goods are stored prior to being sold. It can be an outdoor or indoor area. Sometimes, it can be both an indoor and outdoor space.
How does manufacturing avoid bottlenecks in production?
You can avoid bottlenecks in production by making sure that everything runs smoothly throughout the production cycle, from the moment you receive an order to the moment the product is shipped.
This includes both planning for capacity and quality control.
Continuous improvement techniques such Six Sigma can help you achieve this.
Six Sigma Management System is a method to increase quality and reduce waste throughout your organization.
It is focused on creating consistency and eliminating variation in your work.
Statistics
- Many factories witnessed a 30% increase in output due to the shift to electric motors. (en.wikipedia.org)
- [54][55] These are the top 50 countries by the total value of manufacturing output in US dollars for its noted year according to World Bank.[56] (en.wikipedia.org)
- According to the United Nations Industrial Development Organization (UNIDO), China is the top manufacturer worldwide by 2019 output, producing 28.7% of the total global manufacturing output, followed by the United States, Japan, Germany, and India.[52][53] (en.wikipedia.org)
- (2:04) MTO is a production technique wherein products are customized according to customer specifications, and production only starts after an order is received. (oracle.com)
- Job #1 is delivering the ordered product according to specifications: color, size, brand, and quantity. (netsuite.com)
External Links
How To
Six Sigma and Manufacturing
Six Sigma is defined by "the application SPC (statistical process control) techniques to achieve continuous improvements." It was developed by Motorola's Quality Improvement Department at their plant in Tokyo, Japan, in 1986. Six Sigma is a method to improve quality through standardization and elimination of defects. This method has been adopted by many companies in recent years as they believe there are no perfect products or services. Six Sigma aims to reduce variation in the production's mean value. This means that you can take a sample from your product and then compare its performance to the average to find out how often the process differs from the norm. If there is a significant deviation from the norm, you will know that something needs to change.
Understanding the nature of variability in your business is the first step to Six Sigma. Once you have this understanding, you will need to identify sources and causes of variation. This will allow you to decide if these variations are random and systematic. Random variations occur when people make mistakes; systematic ones are caused by factors outside the process itself. Random variations would include, for example, the failure of some widgets to fall from the assembly line. You might notice that your widgets always fall apart at the same place every time you put them together.
Once you have identified the problem, you can design solutions. This could mean changing your approach or redesigning the entire process. To verify that the changes have worked, you need to test them again. If they don't work you need to rework them and come up a better plan.