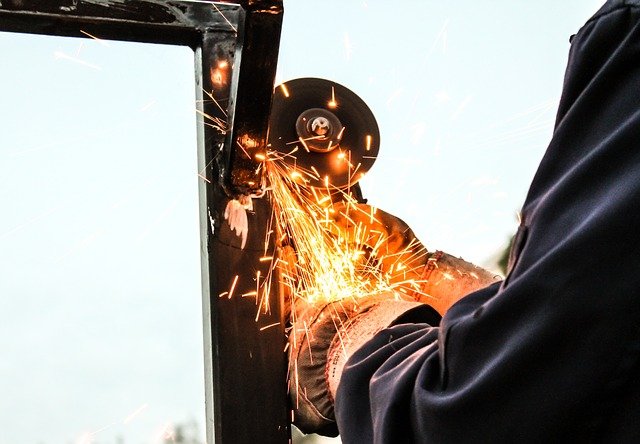
Structure engineers are among the most highly paid professions. The salary of structural engineers is related to the demand for them. A typical requirement for structural engineers is a minimum of a bachelor's level. They should also have at least one year of experience in this field. They could work for a utility company, engineering consulting firm, or construction company. Some structural engineers might even start their own business.
Structural Engineers design structures that can withstand severe stresses. They should also know the properties different materials. They may also be asked to participate in competitive bidding. They need to have project management and communication skills. They should also be proficient in computer software. They might need to work overtime in order to meet deadlines. They may also be able to travel for clients projects that are not in their immediate area.
Structure engineers are usually full-time workers. Although they are able to work full-time, many structure engineers also work part-time. They can use the company car and receive extended health benefits if they work for a company. They might also be eligible to participate in an employee share-ownership plan. The salary of a structural engineer can be increased by changing employers and obtaining an advanced degree. The annual salary for structural engineers ranges from $59,000 to 108,000.
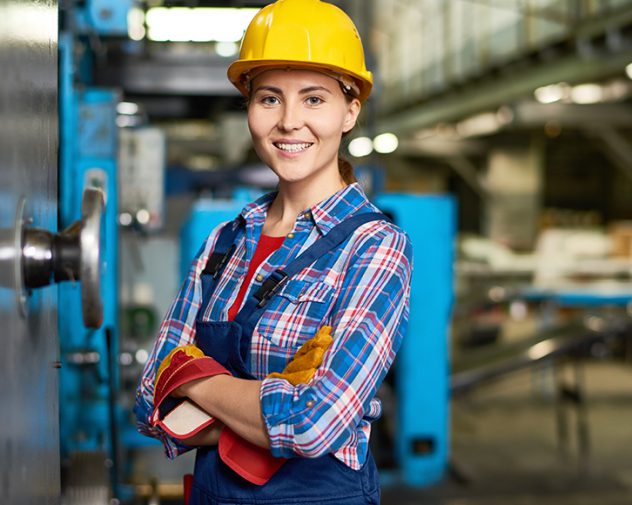
The salaries for structural engineers vary across the United States. A structural engineer in San Francisco makes $147,822 per year. District of Columbia earns the second-highest salary, with an average of $146.683. Deer Park (CA) is the third highest paying area, with an average salary $111562.
The average salary for a structures engineer in Oslo, Norway is kr 765 026 per year. However, the salary of structural engineers in this city is 8% higher than the average salary in Norway. The cost to live is also associated with the salary of structural engineering engineers.
The typical work hours of structural engineers are Monday through Friday, 9:00 am to 5:00pm. They can also work nights, weekends, and holidays. They may also visit construction sites to observe the progress. They will need communication skills to communicate the designs to their clients. They also need to be able to use computer-aided design (CAD) software to visualize their finished parts.
An experienced engineer can work with a structural engineer as an assistant. He or she must complete supervised training before they are able to work alone. Structural engineers can also gain certification through an apprenticeship program. They must have at minimum four years experience in the field. After they have gained enough experience, they can apply directly for employers.
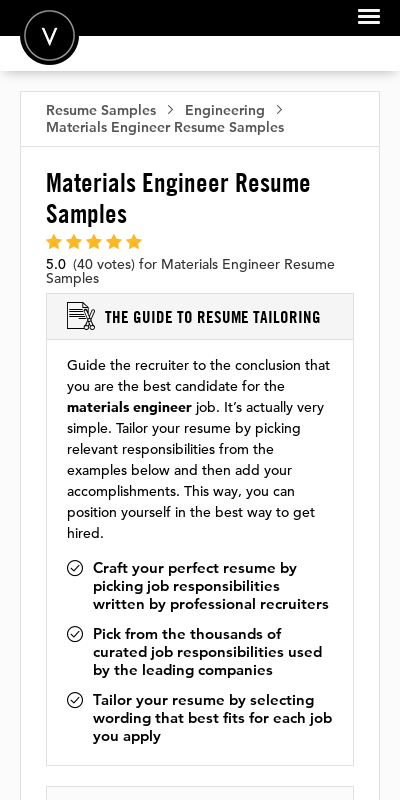
Most structural engineers make $42 an hour. If you are a structural engineer, your salary can increase if you work harder and gain experience. Senior structural engineers are rewarded with the highest salaries. You can also join the Institution of StructE which recognizes excellence within the field.
The total salary of a structural engineer includes the employee's salary, bonus, or profit sharing. The average bonus amount is $3,179
FAQ
What is it like to manage a logistics company?
It takes a lot of skills and knowledge to run a successful logistics business. Good communication skills are essential to effectively communicate with your suppliers and clients. It is important to be able to analyse data and draw conclusions. You must be able manage stress and pressure under pressure. You must be creative and innovative to develop new ideas to improve efficiency. You will need strong leadership skills to motivate and direct your team members towards achieving their organizational goals.
You must be organized to meet tight deadlines.
How does a production planner differ from a project manager?
The major difference between a Production Planner and a Project Manager is that a Project Manager is often the person responsible for organizing and planning the entire project. While a Production Planner is involved mainly in the planning stage,
What skills do production planners need?
Production planners must be flexible, organized, and able handle multiple tasks. Communication skills are essential to ensure that you can communicate effectively with clients, colleagues, and customers.
Are there ways to automate parts of manufacturing?
Yes! Since ancient times, automation has been in existence. The Egyptians created the wheel thousands years ago. Today, robots assist in the assembly of lines.
Actually, robotics can be used in manufacturing for many purposes. These include:
-
Line robots
-
Robot welding
-
Robot painting
-
Robotics inspection
-
Robots that make products
There are many other examples of how manufacturing could benefit from automation. For example, 3D printing allows us to make custom products without having to wait for weeks or months to get them manufactured.
What is the importance of logistics in manufacturing?
Logistics are an integral part any business. They enable you to achieve outstanding results by helping manage product flow from raw materials through to finished goods.
Logistics plays a significant role in reducing cost and increasing efficiency.
Is automation necessary in manufacturing?
Automation is essential for both manufacturers and service providers. It allows them to offer services faster and more efficiently. It also helps to reduce costs and improve productivity.
What is the job of a manufacturer manager?
A manufacturing manager must ensure that all manufacturing processes are efficient and effective. They should be alert for any potential problems in the company and react accordingly.
They should also be able and comfortable communicating with other departments like sales and marketing.
They must also keep up-to-date with the latest trends in their field and be able use this information to improve productivity and efficiency.
Statistics
- You can multiply the result by 100 to get the total percent of monthly overhead. (investopedia.com)
- According to the United Nations Industrial Development Organization (UNIDO), China is the top manufacturer worldwide by 2019 output, producing 28.7% of the total global manufacturing output, followed by the United States, Japan, Germany, and India.[52][53] (en.wikipedia.org)
- It's estimated that 10.8% of the U.S. GDP in 2020 was contributed to manufacturing. (investopedia.com)
- Many factories witnessed a 30% increase in output due to the shift to electric motors. (en.wikipedia.org)
- In 2021, an estimated 12.1 million Americans work in the manufacturing sector.6 (investopedia.com)
External Links
How To
How to Use Lean Manufacturing for the Production of Goods
Lean manufacturing (or lean manufacturing) is a style of management that aims to increase efficiency, reduce waste and improve performance through continuous improvement. It was developed by Taiichi Okono in Japan, during the 1970s & 1980s. TPS founder Kanji Takoda awarded him the Toyota Production System Award (TPS). Michael L. Watkins published the "The Machine That Changed the World", the first book about lean manufacturing. It was published in 1990.
Lean manufacturing can be described as a set or principles that are used to improve quality, speed and cost of products or services. It emphasizes the elimination of defects and waste throughout the value stream. Lean manufacturing is also known as just in time (JIT), zero defect total productive maintenance(TPM), and five-star (S). Lean manufacturing eliminates non-value-added tasks like inspection, rework, waiting.
Lean manufacturing improves product quality and costs. It also helps companies reach their goals quicker and decreases employee turnover. Lean manufacturing is a great way to manage the entire value chain including customers, suppliers, distributors and retailers as well as employees. Many industries worldwide use lean manufacturing. Toyota's philosophy is a great example of this. It has helped to create success in automobiles as well electronics, appliances and healthcare.
Five fundamental principles underlie lean manufacturing.
-
Define value - Find out what your business contributes to society, and what makes it different from other competitors.
-
Reduce Waste - Remove any activity which doesn't add value to your supply chain.
-
Create Flow: Ensure that the work process flows without interruptions.
-
Standardize & Simplify - Make processes as consistent and repeatable as possible.
-
Build Relationships- Develop personal relationships with both internal as well as external stakeholders.
Lean manufacturing is not a new concept, but it has been gaining popularity over the last few years due to a renewed interest in the economy following the global financial crisis of 2008. To increase their competitiveness, many businesses have turned to lean manufacturing. Some economists even believe that lean manufacturing can be a key factor in economic recovery.
With many benefits, lean manufacturing is becoming more common in the automotive industry. These include higher customer satisfaction levels, reduced inventory levels as well as lower operating costs.
You can apply Lean Manufacturing to virtually any aspect of your organization. Because it makes sure that all value chains are efficient and effectively managed, Lean Manufacturing is particularly helpful for organizations.
There are three main types in lean manufacturing
-
Just-in-Time Manufacturing (JIT): This type of lean manufacturing is commonly referred to as "pull systems." JIT stands for a system where components are assembled on the spot rather than being made in advance. This approach is designed to reduce lead times and increase the availability of components. It also reduces inventory.
-
Zero Defects Manufacturing (ZDM): ZDM focuses on ensuring that no defective units leave the manufacturing facility. Repairing a part that is damaged during assembly should be done, not scrapping. This is true even for finished products that only require minor repairs prior to shipping.
-
Continuous Improvement (CI: Continuous improvement aims to increase the efficiency of operations by constantly identifying and making improvements to reduce or eliminate waste. It involves continuous improvement of processes, people, and tools.